Efficient and environmentally friendly lime protection that is reflected in your operations and carbon footprint
For more than 100 years, the Swarovski brand has been synonymous with creativity, ingenuity, and cutting-edge crystal technology. The consistent further development of their unique cutting expertise has made Swarovski the world's leading manufacturer of cut crystal, natural and artificial gemstones. With a sustainable choice of energy sources, efficient use of renewable energy, and green, innovative energy technologies, the company consistently works to minimize environmental impact and optimize energy efficiency. In this context, the domestic hot water heating system at the factory was renovated - while the waste heat from the compressor station was used as an energy source to heat the water.
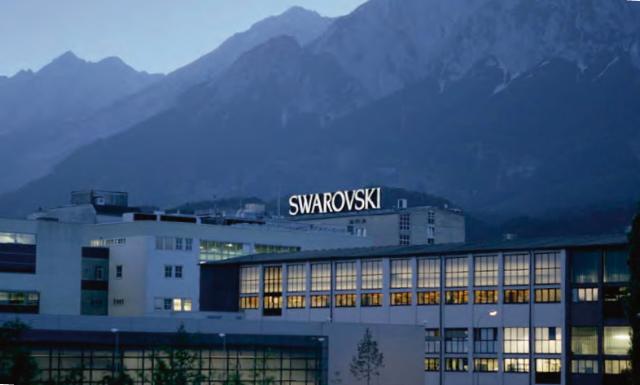
The process water comes from the plant's deep well, is very hard, and deposits limescale when heated, which leads to costly malfunctions in the technical systems even after a short period of operation and acts as a costly energy brake. The challenge for lime protection technology was, on the one hand, to keep treatment costs as low as possible due to the enormous volumes of water that are converted and, on the other hand, to comply with environmental regulations due to the direct discharge of wastewater.
Conventional treatment methods such as softening via ion exchange or dosing inhibitors fulfill neither the economic nor the environmental requirements, as large amounts of treatment chemicals such as salts and polyphosphates must be added to the water and wastewater and are therefore generally excluded.
Tried and tested - and fulfills all rules and regulations
In the search for an effective and economical limescale protection solution that also fulfills the high requirements for drinking water quality with as little environmental impact as possible, the responsible technicians came across the new limescale protection technology in the form of BIOCAT systems from WATERCryst.
BIOCAT limescale protection systems with Watercryst-technology fulfill the strict regulations of DVGW worksheets W510 and W512 regarding their effective limescale protection. DVGW-type test certificates are available for the most frequently used large-scale systems (KS 3000, KS 8000, KS 11000, KS 14000), which confirm the technical and hygienic suitability of the systems for use in drinking water.
The systems also fulfil the generally recognized technical regulations and can therefore be used without any concerns in accordance with the Drinking Water Ordinance. As there is no need for chemical treatment agents, the composition of the drinking water is not changed and the existing strict environmental regulations for direct discharge can be easily complied with.
Plate heat exchangers free from limescale
Without effective measures to protect against limescale, experience shows that plate heat exchangers calcify so much within three to four months, depending on the local water quality and the amount of water consumed, that the plate heat exchangers often can no longer be flushed free of limescale and must be replaced. The deterioration in heat transfer performance due to the gradual build-up of limescale in the heat exchanger was an important indicator of when it was time to take appropriate action.
In this respect, the BIOCAT systems were surprised after only a few months of operation, as no signs of a decrease in transfer performance could be observed. As part of the mandatory technical audit, the BIOCAT system's effectiveness in terms of limescale protection was also checked: despite the large volumes of water transferred and the high temperatures, no limescale deposits could be found in either the plate heat exchangers or the storage tank. This result was also confirmed by further inspections in the following years.
Major savings in operations and CO2 emissions
The responsible technicians at the Swarovski factory are not only enthusiastic about the great process success, which has continued unabated for more than six years but also about the cost savings achieved, especially about CO2 dosing, which was already very cost-effective. The system has already paid for itself, and the operating cost savings realized are at least EUR 4,500 per year on average.
According to the Swarovski example, if BIOCAT limescale protection technology is evaluated in terms of a sustainable investment policy and operational management over 20 years of use, savings of around EUR 86,000 and 51 tons of CO2 can be achieved based on the factory's current use of a two-shift operation. Add to this the fact that the performance potential of the BIOCAT lime protection system is far from fully utilized. At full capacity (which corresponds to a three-shift operation), the savings potential rises to 112 tons of CO2 and EUR 150,000.